3 retractable roof projects open up special construction considerations
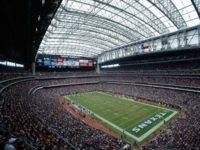
While a few years ago it might have seemed like massive structures with movable parts were only achievable in futuristic movies, they are becoming commonplace on high-profile, design-centric spaces that cater to both indoor and outdoor events.
What’s not commonplace is the special construction considerations required to build them.
A retractable roof provides shelter from the elements and makes a structure usable year round, especially for sports and entertainment venues. The number of stadiums with operable roofs has slowly increased since the opening of Chase Field in Phoenix in 1998. That breakthrough has been followed by other retractable-roof ballparks such as Safeco Field, home of the Seattle Mariners, and the Indianapolis Colts’ Lucas Oil Stadium.
While everyone knows that these flexing, morphing structures provide high-wattage architectural appeal and flexibility in all kinds of weather, their construction requires extra time and specialized know-how. In the three projects below, Construction Dive details the challenges and rewards of structures with ultra-customized mobile roofs.
Globe Life Field
General contractor: Manhattan Construction
Design architect: HKS

When it’s complete early next year, the 1.8 million-square-foot home of the Texas Rangers will include a retractable roof for climate control during the hot summer months that will operate on a mechanism much like a train on a railroad track.
With such a unique feature, the roof required unusually long structural steel spans of more than 600 linear feet, according to Manhattan Construction Vice President of Operations Jim Cuddihee. Because it was not feasible to use one crane to lift such long members, it was constructed in segments that were lifted into place one at a time using a specialized hydraulic system from Enerpac.
The SyncHoist system allowed the trusses to be assembled on the ground and then hydraulically lifted and put into place with one crane instead of building them up in the air.
To prepare for the roof installation, Manhattan Construction workers built temporary supports to hold the installed pieces in place until the entire span was connected and could support itself, said Cuddihee. The process was not without challenges, especially the need for limiting construction work below while the roof trusses are being moved.
“It is a complicated scheduling dance to provide space and clearance so our crane operators can put the spans in place on one side of the stadium while construction activity down below progresses on the other side,” he said. “The most important part is addressing the unique safety considerations with this type of activity, including training workers about the unique safety precautions while working with heights in, around and below.”
The movable nature of the roof also made it much more complicated and heavy than a fixed roof, Enerpac Product Line Director of Heavy Lifting Pete Crisci told Construction Dive. Several SyncHoist features helped smooth installation. The system’s wireless communication allowed Enerpac engineers to control pieces of steel some 200 feet in the air and precisely position it down to the millimeter from an iPad-like screen on the ground. The final truss of the 5.5-acre, 9,600-ton retractable roof was lifted into place just a few weeks ago.
While not providing specific cost information for the Globe Life roof installation, Crisci said that modular roofing trusses in general generate cost savings by requiring less equipment, crews and time. “From a speed and efficiency standpoint,” he said, “we can do the work much more quickly and safely.”
In use across the world for 15 years, the SyncHoist system was also used to install the roofs of the Atlanta Falcons’ Mercedez Benz Stadium, the “Bird’s Nest” Olympic stadium in Beijing, China, and for the renovation of the San Francisco-Oakland Bay Bridge.
Ground-level modular roof construction is ideal for extremely large, complex projects like bridges, power plants and ship building factories, Crisci said.
“One of the things you’re seeing in stadium trends these days is that they are getting much bigger and more elaborate so the designs are quite complex,” Crisci said. “This means that traditional construction methods of erecting individual roof components in the air isn’t really the best way to do it anymore, given the sheer size of the large roof trusses on these stadiums.”
The Shed
Construction manager: Sciame Construction
Lead architect: Diller Scofidio + Renfro
Collaborating architect: Rockwell Group
Structural and façade engineer: Thornton Tomasetti

The unique architectural appeal of the Shed is only one reason that it’s seen as one of New York City’s most distinctive cultural landmarks. The 200,000-square-foot art and performance space that opened in April in Hudson Yards boasts eight levels that include two large gallery spaces, a theater, a rehearsal space and an artists’ lab, but its most recognizable feature is its bubble-like exterior that rolls onto an outdoor plaza, creating additional space for performances and art shows.
The Shed’s shell is made of an exposed steel frame clad in three layers of translucent ETFE polymer material, which has the thermal properties of insulating glass at a fraction of the weight, according to Sciame Construction CEO Frank Sciame.
The 4,000-ton shell sits on eight 6-foot-tall solid cast steel wheels; the total surface contact for each wheel carrying 1 million pounds is about the size of a palm of a human hand, Sciame told Construction Dive. The shell’s movement is absolutely silent and takes only five minutes to fully deploy.
Although contractor Sciame Construction has worked on several other high-profile projects like the restoration of Manhattan’s historic Trinity Church, the Shed required special consideration.
“The scale, complexity and precision required by the Shed project required close collaboration in the pre-planning, engineering and construction processes from start to finish,” Sciame said.
Working with structural and façade engineer Thornton Tomasetti and lead architect Diller Scofidio + Renfro, Sciame led a worldwide design-assist bid process, including the construction of multiple full-size mock-ups, to identify the right firm for the extensive engineering and complex fabrication, installation, and on-site logistics. A similar process was followed for many other aspects of the design including the shell’s façade. The entire process took 40 months from start to finish, he said.
The biggest challenge for the contractor came in the preconstruction phase, when Sciame was heavily involved in the design-assist process for the steel and kinetic systems to move the building and its glass walls, he said. Site logistics were also a major challenge. Crane placements and other critical logistical operations had to be carefully sequenced and scheduled with contractors on nearby projects, Friends of the High Line and other groups.
“Sitting on top of a platform built over rail yards, bordered by the High Line to the south, an office building to the east, the 30th Street pedestrian plaza to the north, and being physically connected to 15 Hudson Yards to the west, the Shed was literally surrounded by major projects under construction at the same time,” Sciame said.
Hokkaido Ballpark
General contractor: Obayashi
Architect: HKS

Set to break ground early next year, the $530 million ballpark in Hitahiroshima, Japan, will feature a signature glass wall and sliding roof, allowing the park to be fully enclosed during the area’s frigid winters and still support natural grass.
It will be the second stadium in Japan with a retractable roof; Yafuoku Dome, opened in 1993, was the first.
With a planned opening in 2023, the 35,000-seat venue for Japan’s Nippon-Ham Fighters Baseball Club will set a new bar for baseball venues in the country, according to Building Design + Construction. The design by HKS features a massive gabled retractable roof evocative of old-style homes in the area, with an expansive glass wall encasing the outfield.
The stadium will stand four stories high, with the field one floor below ground level. Hot baths in the upper deck in left field are also part of the plan. The playing surface will be symmetrical, something unheard of at Japanese ballparks until Hiroshima’s Mazda Stadium opened in 2009, according to Japan Times.
Much like new stadium projects in the U.S., Hokkaido will be surrounded by a live entertainment district.
In a country where major stadiums are nearly 100% reliant on public transportation, the Fighters’ stadium is expected to have parking for 3,000 to 4,000 vehicles. Kitahiroshima’s local government is also looking to have a new station built close to the park.
This article was originally written by Jenn Goodman and appeared here.
Comment (0)